
Gain control of fixture sets and resets when you engage HRG’s space planning and process improvement experts to simplify and streamline coordination and installation while saving resources and costs.
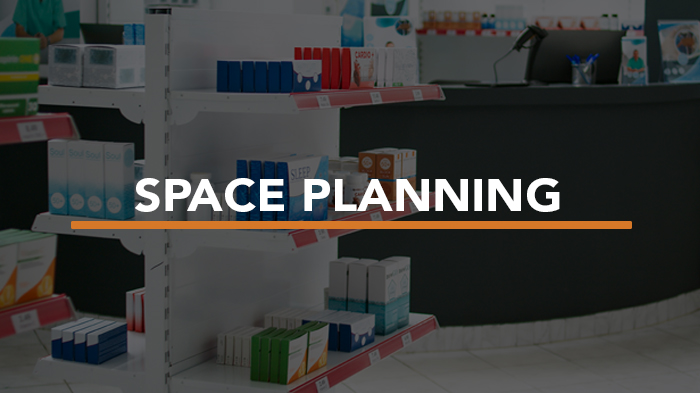
Looking for efficient, consistent, and reliable space planning services? Whether you’re a brand, retailer, or fixture manufacturer — we’re a one-stop shop for your space planning needs. HRG analysts can build anywhere from a one-foot to twenty-foot or larger fixture planogram. For one chain, we validated fit in nearly 700 planograms for just one season. Likewise, for brands, we create planograms for each of your retail partners to ensure consistency across outlets and channels.
Ensure a successful implementation when you rely on HRG’s retail expertise combined with our knowledge of space planning software to establish reliable business rules. Using planogram files provided by a retailer or a brand, our expert analysts extract the dimensions and number of trays, graphics, holders, clips, and space savers used in a new configuration. We also validate that everything the brand expects to fit on a wall or display will indeed fit, a must for efficient and effective at-shelf execution.
Simplify and accelerate the installation process with this dynamic merchandising tool. This animated depiction of product placement on shelves, fixture assembly, or a full reset is easy to comprehend so your vision will come to life at shelf without error. Static renders are also available for dimensional visuals to enhance buyer presentations and sell sheets.
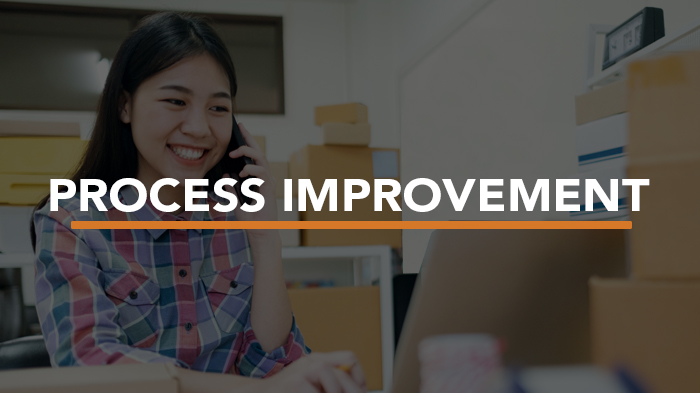
Streamline fixture sets and resets with HRG’s proven tools and technology to help save costs, maximize sustainability, and minimize downtime and missed sales. HRG’s experienced project managers coordinate with all stakeholders so resets run smoothly from beginning to installation.
Avoid costly mistakes with robust Custom Reorder Websites — a central location to manage aftercare with easy access to reorder all parts, including images of them for ease of use. Pieces and parts are stored for reference, so everyone across the supply chain can save money and move closer to sustainability goals by repurposing pieces already on hand.
Ensure a smooth and efficient fixture reset with the right training materials. Store associates or merchandising crews have a variety of learning styles, so offering a mix of videos, installation manuals, and one-sheets can speed at-shelf execution.
TESTIMONIALS
"We have been thrilled to make the leap to using HRG as our space planning partner. Their expertise, attention to detail, and partnership have made our ability to finalize our space plans and determine our fixture needs seamless. The HRG team has adapted to changes and helped build new processes from scratch to improve deliverables to our retail partners."
Jen Olson
Former Vice President Sales

"We're very pleased with everything Hamacher delivered, as is our retailer client. It was a collaborative relationship and I'm impressed by all that was accomplished. HRG's flexibility and willingness to stretch their abilities to meet our needs and the needs of our client was instrumental in the overall success of this project. I hope we have the opportunity to work together again."
Jeff Kildow
Business Development

"I would absolutely give you a GREAT referral!!!! There is no question in my mind how valuable an organization like your company is with fixtures, planograms, reorders and mapping of effective processes. Your proven history and work ethic speak for themselves."
Fixture Procurement Manager - Nationwide Chain Retailer
“HRG is the key reason our Mineral Fusion display program was a success at BWX. I could not have done it without your support, and should I ever be in the position again to need a resource company to partner with in my career, HRG will of course be my first choice. I always enjoyed working with your team of professionals. It was an easy partnership and a key one."
Lori Silva
former Packaging & Display Merchandising Design Director
BWX USA
RESOURCES
Info Sheets
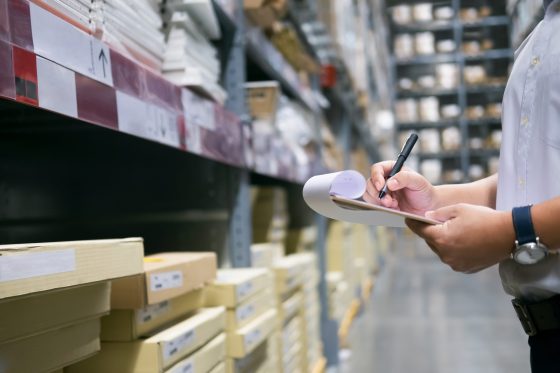
Operations Efficiencies
A local custom injection molding company located in Pewaukee, Wisconsin was in the process of bidding on a project to provide all of the fixtures necessary for a complete overhaul of a big box retailer’s cosmetic department, when they realized they were unable to open or read the space planning files that the retailer had provided.
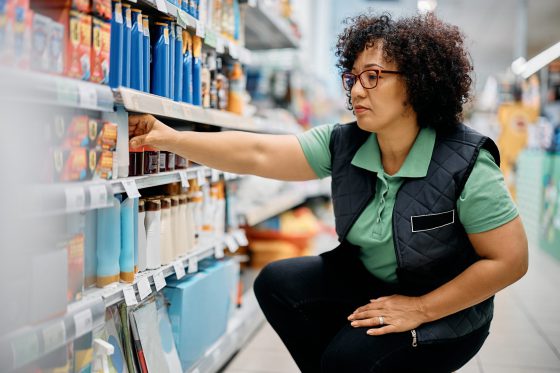
Turnkey Training
A local custom injection molding company located in Pewaukee, Wisconsin was in the midst of preparing their bid on a project to provide fixtures for a complete overhaul of a national big box retailer’s cosmetic department when they determined they needed complete training materials to help store associates install the fixture components.
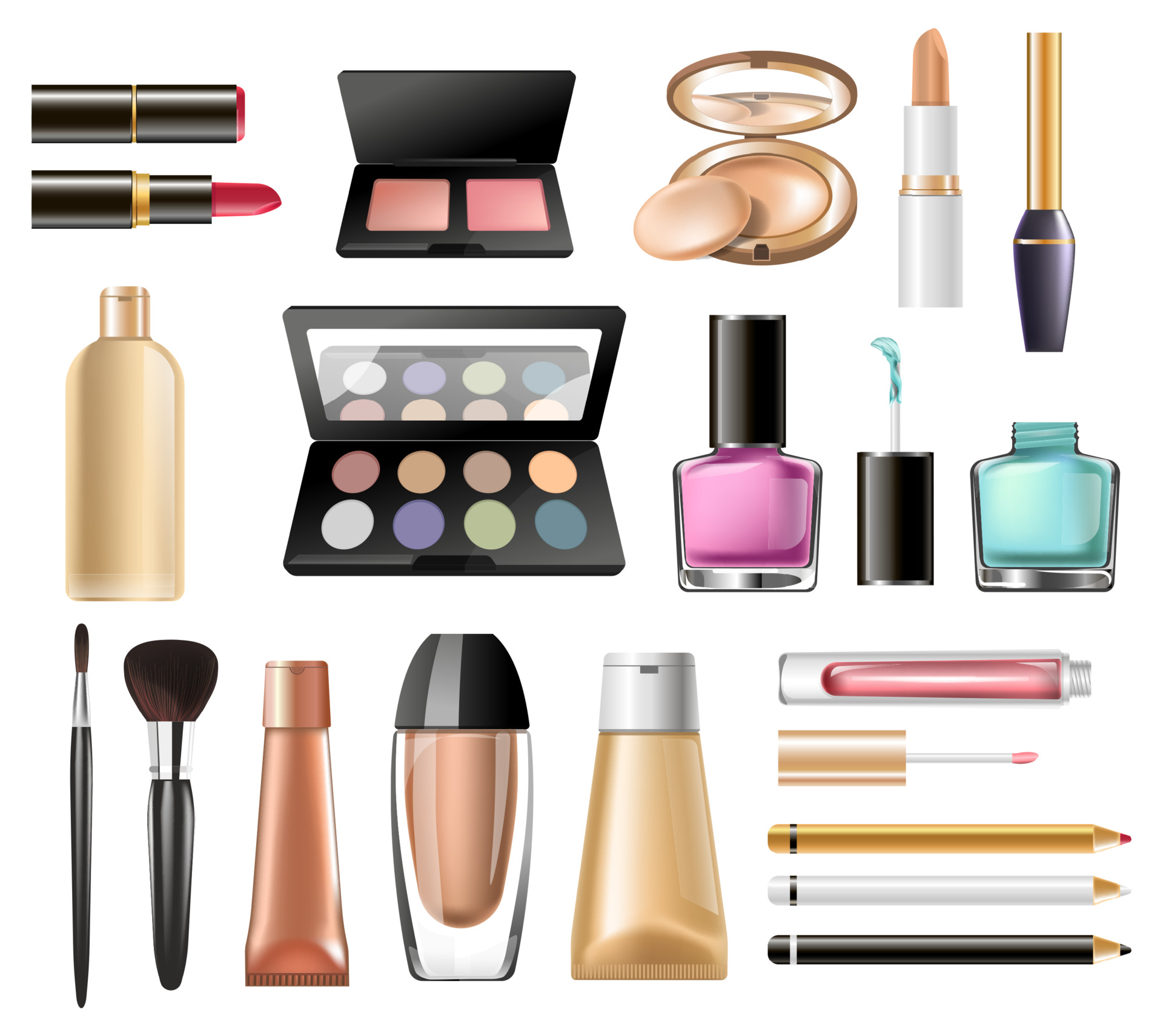
Beauty brands take steps for success
by Megan Moyer, corporate marketing manager, as appeared in Inside Beauty for Drug Store News Beauty brands
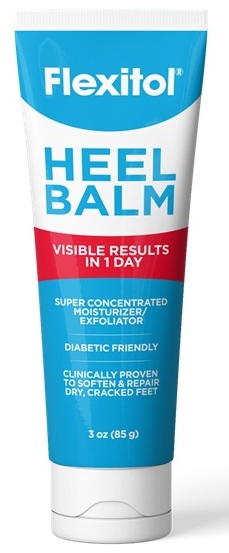
Flexitol brings innovation and efficacy to therapeutic skin care
by Megan Moyer, corporate marketing manager, as appeared in Inside Beauty for Drug Store News Like many
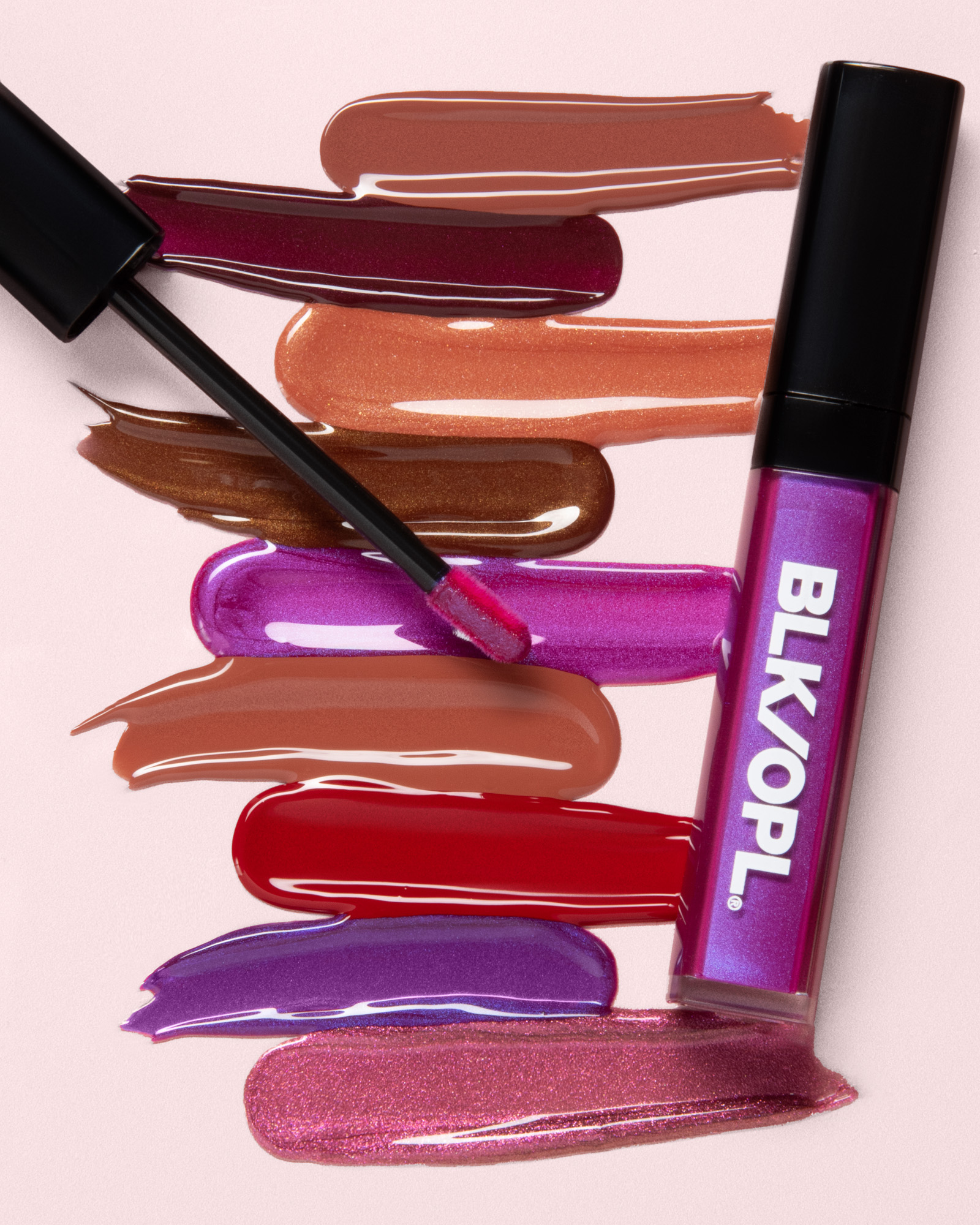
Black Opal has stood the test of time
by Megan Moyer, corporate marketing manager, as appeared in Inside Beauty for Drug Store News
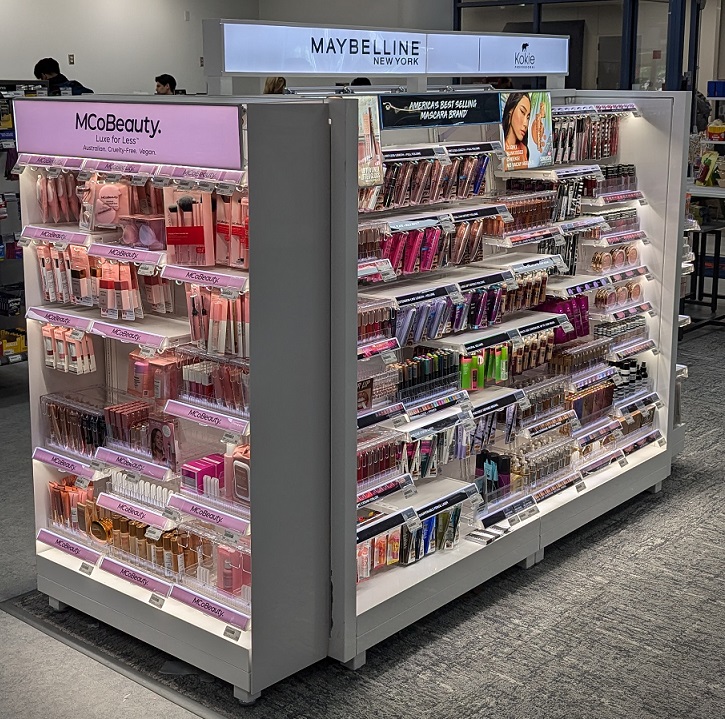
Follett strives to meet Gen Z needs
by Megan Moyer, corporate marketing manager, as appeared in Inside Beauty for Drug Store News What was